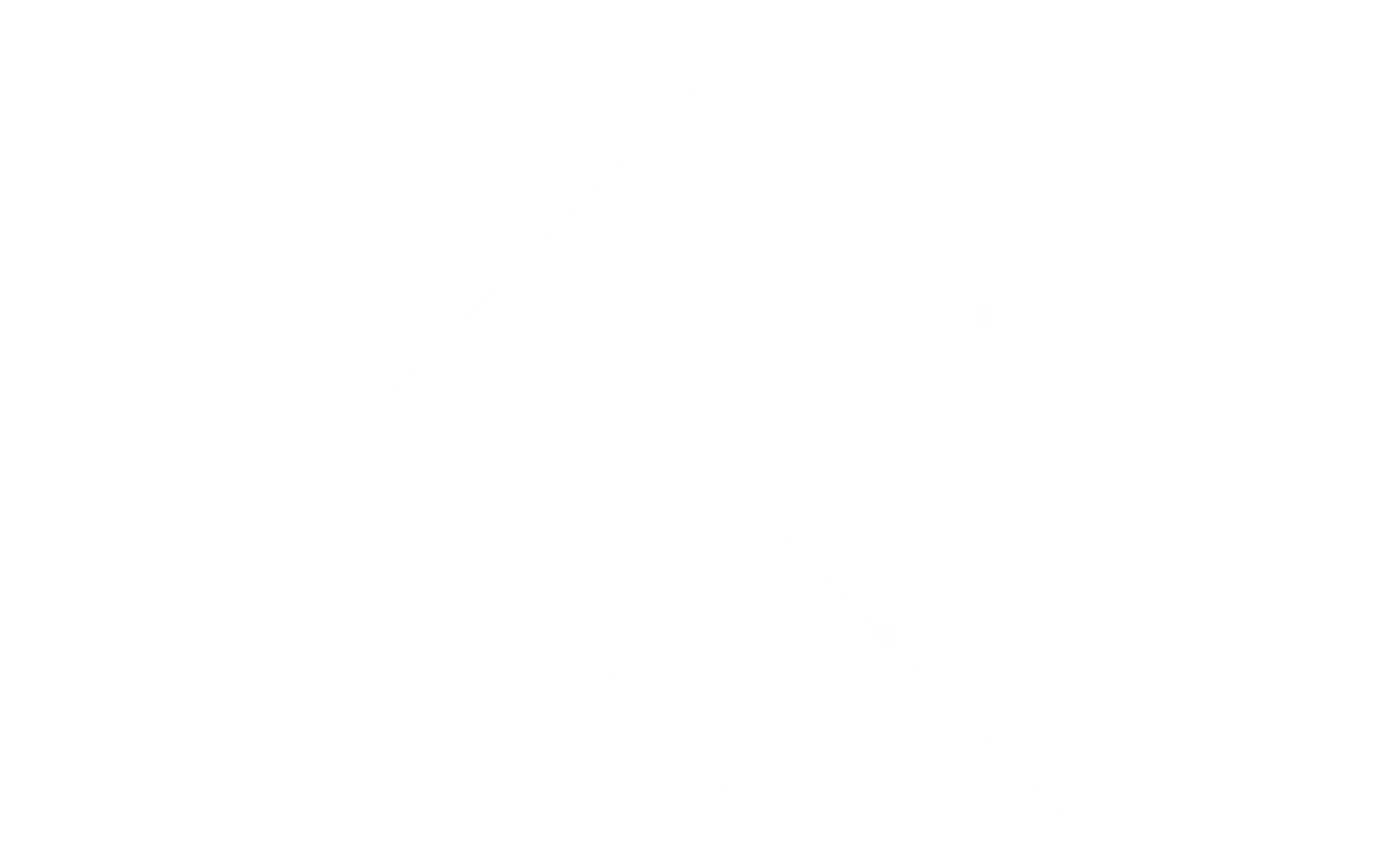
PROFILES IN INNOVATION : APC

AUTOMATIC POWER CALIBRATION
Industry First to implement true process control by measuring the OUTPUT of the laser
Innovation Type
Breakthrough
Innovation Driver
Market / Need
Technology
Laser, optics, sensors, system software
Key Points
Key process control feature to improve rate of adoption for lasers in a high growth market opportunity
Industry
Semiconductor
-
Semiconductor manufacturing depends on continuous improvement to drive yield up and cost down. Six Sigma and other quality initiatives are key drivers to meet these objectives. Lasers were being explored for a number of manufacturing processes. They would have to support tight process windows to be accepted as preferred process.
-
A robust and reliable means of monitoring laser output was a requirement for mandated quality standards. The typical laser process parameter was -input- current. Setting current will not guarantee process performance as the laser output, while a function of current, can vary considerably as a result of component specifications, aging, service issues or even catastrophic failure.
-
The process parameter which directly interacts with the part is the laser -output- in watts. An in-line sensor was developed to measure the full output power of the laser as close as possible to the part being processed. The GUI provides an intuitive and simple means for process monitoring on the factory floor.
-
This option became a standard feature for all laser systems supplied to the semiconductor industry. The process measurement, logging and reporting were automated for seamless integration with existing MES (Manufacturing Execution Systems) software.
Fig. 1 - Laser output power profile in watts vs. current
Fig. 2 - Process parameter lifetime curve for repeatable process control